I was also interested in this problem and tried to solve it, but the current EnergyPlus doesn't allow for variable flow of condenser water. Practically, there are two ways to control Condenser Loop: by varying air flow rate of cooling tower fan or by varying water flow rate of condenser pump, and I have actually designed a building with variable condenser loop, but EnergyPlus is only designed to vary fan air flow rate.
Chiller Flow Mode
is for chilled water. This flow mode doesn't impact condenser water flow, but it's not a big deal. The fatal problem is that the condenser water flow rate is forced to be constant by Reference Condenser Fluid Flow Rate
or Design Condenser Fluid Flow Rate value
in any chiller objects. I could not override this condenser water flow rate even with EMS. The problem found in the post two years ago remains unresolved. I hope future updates to EnergyPlus will fix this problem.
However, there is a way to know the flow rate and energy rate of condenser water pump when the flow rate is variable. I have come up with the following approach.
- Use
CoolingTowr:SingleSpeed
, and set Capacity Control
to FluidBypass
. - Add
Cooling Tower Mass Flow Rate
, Cooling Tower Bypass Fraction
and Pump Electricity Rate
in OutputVariable
.
Actually, FluidBypass
does not save energy at partial load, but the "hypothetical" variable pump flow rate can be manually calculated from hourly output variables. (Capacity Control
has only two choices, FanCycling
and FluidBypass
, which also indicates that EnergyPlus does not assume variable condenser water.)
Variable condenser pump flow rate [kg/s] = Cooling Tower Mass Flow Rate
× (1 - Cooling Tower Bypass Fraction
)
Variable condenser pump energy rate [W] = Pump Rated Electricity Rate × FractionFullLoadPower
FractionFullLoadPower can be calculated using the following equation in I/O Reference and EngineeringReference. I think the Part Load Ratio is the same as (1 - Cooling Tower Bypass Fraction
).

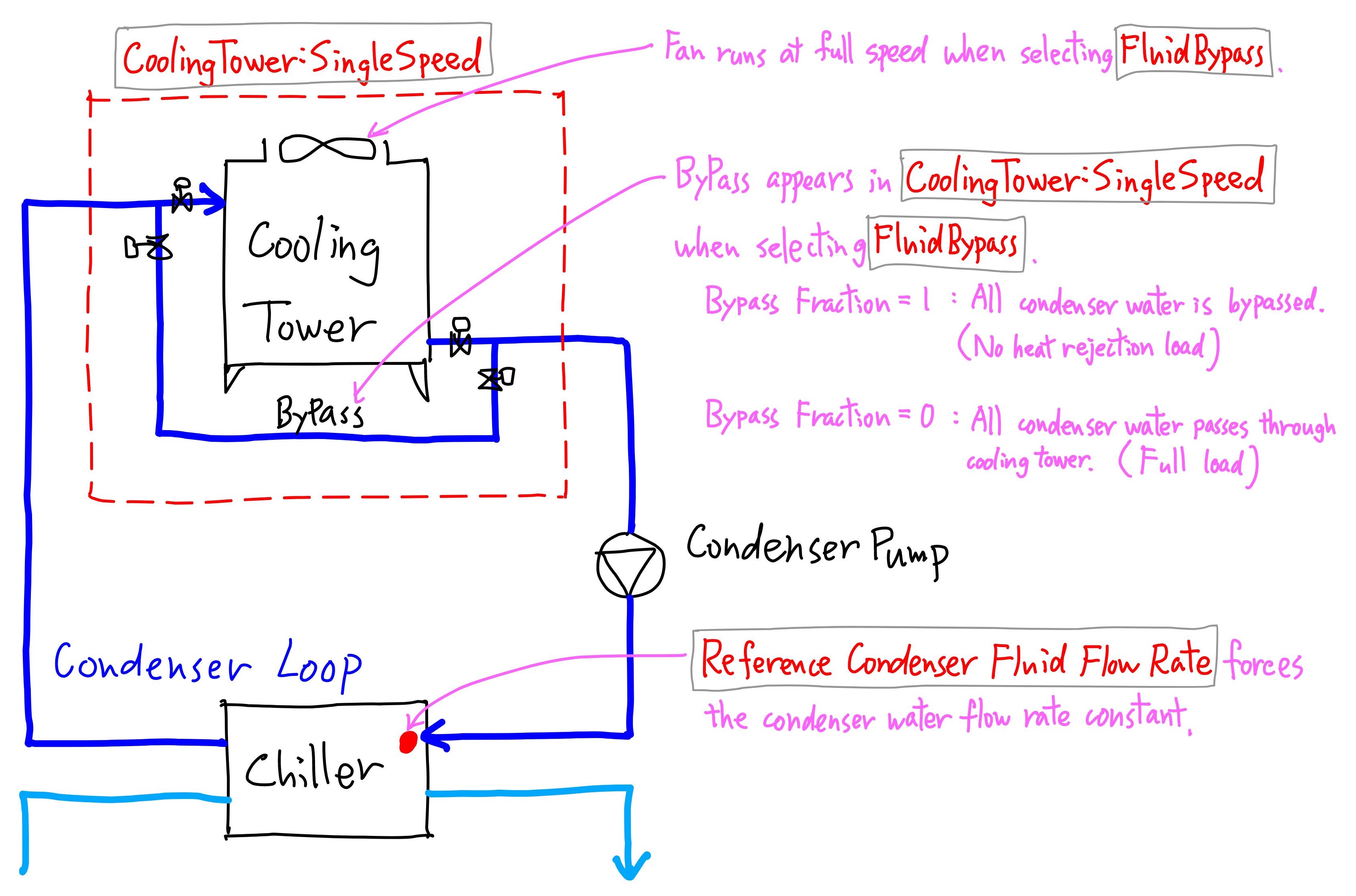
Strictly speaking, when the condenser pump flow rate is variable (reduced), the pump shaft power transmitted to the condenser water is also reduced. The cooling load is reduced, but the cooling tower fan air flow rate is constant, so the actual variable pump flow rate should be a little less than the manually calculated flow rate.
Here is a reference IDF file (v9.4.0). One thing to add is that the setpoint of condenser water loop should be set at entering or leaving temperature of the condenser water by SetpointManager:Scheduled
. Some ExampleFiles use OutdoorAirWetBulb
as a setpoint by SetpointManager:FollowOutdoorAirTemperature
, but it's not an appropriate setting. Since the condenser water temperature doesn't reach exactly the same value as outdoor air wet bulb temperature, the condenser loop can't meet the setpoint, and the bypass fraction always becomes 0.